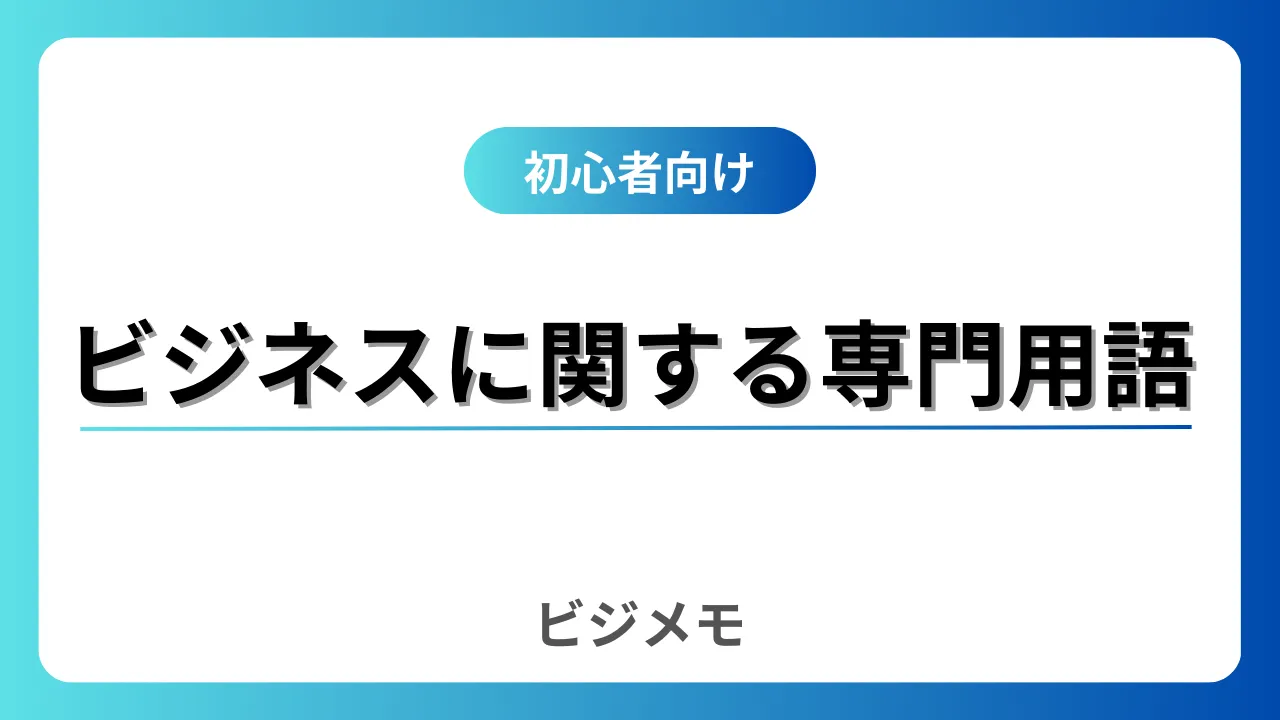
PPAP(Production Part Approval Process)とは
PPAP(Production Part Approval Process)は、自動車産業を中心に用いられる部品承認プロセスです。サプライヤーが顧客要求を満たす製品を安定して供給できる能力を証明するために不可欠な仕組みであり、品質保証の基盤となります。
このプロセスは、新製品の立ち上げ時や設計変更時において、部品の品質、性能、生産能力などを包括的に評価することを目的としています。PPAPを通じて、サプライヤーと顧客間のコミュニケーションが円滑になり、誤解や手戻りを防ぐことが可能です。
PPAPの実施は、製品の品質向上、コスト削減、納期遵守に貢献し、最終的には顧客満足度の向上につながります。自動車業界だけでなく、他の製造業においても品質管理の重要な手法として注目されています。
PPAPにおける重要な要素
「PPAPにおける重要な要素」に関して、以下を解説していきます。
- PPAPにおける5つのレベル
- PPAPにおける18の要素
PPAPにおける5つのレベル
PPAPには、サプライヤーから顧客への提出要件に応じて5つのレベルが定義されています。レベルごとに提出するドキュメントやサンプルが異なり、製品のリスクや重要度に応じて適切なレベルを選択することが重要です。
レベルの選択を誤ると、承認プロセスの遅延や追加コストが発生する可能性があるため、顧客との十分な協議が必要です。適切なレベルを選択し、必要なドキュメントを正確に準備することで、スムーズな承認プロセスを実現できます。
レベル | 顧客への提出物 | 備考 |
---|---|---|
レベル1 | 部品保証書のみ | 限定的な要求 |
レベル2 | 保証書と限定サンプル | 顧客指定の要求 |
レベル3 | 保証書と完全サンプル | 標準的な要求 |
レベル4 | 顧客要求に基づく提出 | 顧客個別の要求 |
レベル5 | 完全なドキュメントレビュー | サプライヤー事業所 |
PPAPにおける18の要素
PPAPでは、製品の品質を保証するために18の要素が定義されており、これらの要素を網羅的に評価し、文書化することが求められます。各要素は、設計、材料、プロセス、測定など、製品ライフサイクルの様々な段階をカバーしています。
これらの要素を適切に管理することで、潜在的な問題点を早期に発見し、是正措置を講じることが可能になり、結果として高品質な製品の安定供給につながります。18の要素を理解し、適切に対応することが、PPAP成功の鍵となります。
要素 | 内容 | 目的 |
---|---|---|
設計記録 | 部品図面や仕様 | 設計要件の明確化 |
変更許可 | 設計変更の承認記録 | 変更管理の徹底 |
エンジニアリング承認 | 顧客による設計承認 | 設計妥当性の確認 |
DFMEA | 設計段階でのリスク分析 | 潜在リスクの特定 |
工程フロー図 | 製造工程の流れ | 工程全体の可視化 |
PFMEA | 工程段階でのリスク分析 | 工程リスクの特定 |
管理計画 | 品質管理の方法 | 品質維持の計画 |
測定システム分析 | 測定機器の精度評価 | 測定データの信頼性確保 |
材料試験結果 | 材料の品質試験データ | 材料の適合性確認 |
性能試験結果 | 製品の性能試験データ | 性能要件の充足確認 |
外観基準 | 外観品質の基準 | 外観品質の維持 |
サンプル製品 | 顧客提出用のサンプル | 現物確認の実施 |
サンプル検査結果 | サンプル製品の検査データ | サンプル品質の評価 |
統計的工程管理 | 工程の安定性評価 | 工程能力の維持 |
有資格試験室 | 試験室の認定情報 | 試験結果の信頼性担保 |
寸法結果 | 寸法測定データ | 寸法精度の確認 |
材料報告 | 材料構成の報告 | 材料のトレーサビリティ確保 |
部品保証書 | PPAPの完了証明 | 承認プロセスの完了 |