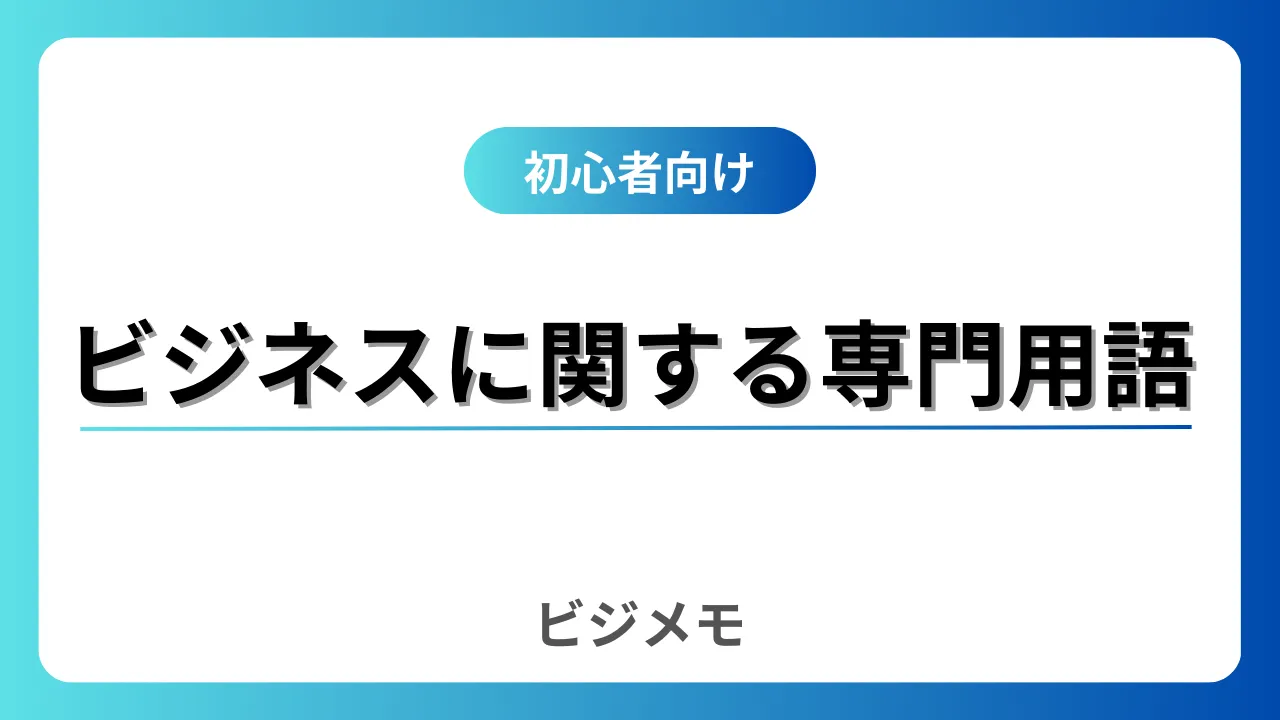
Failure Mode and Effects Analysisとは
FMEA実施のメリット
「FMEA実施のメリット」に関して、以下を解説していきます。
- リスク特定と優先順位付け
- 設計改善と品質向上
リスク特定と優先順位付け
リスク特定と優先順位付けは、FMEAの重要なメリットです。潜在的な故障モードを特定し、それらがシステムや製品に与える影響の大きさを評価することによって、対策を講じるべきリスクを明確にできます。優先順位付けによって、リソースを最も重要なリスクに集中させ、効果的なリスク軽減策を講じることが可能です。
リスクの特定は、製品やプロセスの信頼性を高める上で不可欠です。FMEAを通じて、設計段階や製造プロセスにおける潜在的な弱点を洗い出し、早期に対策を講じることで、後工程での問題発生を未然に防ぎます。これにより、製品の品質向上と顧客満足度の向上に貢献します。
評価項目 | 詳細説明 |
---|---|
故障モード | 具体的な故障状態を記述 |
影響度 | 故障が及ぼす影響の大きさ |
発生頻度 | 故障が発生する可能性の高さ |
検出度 | 故障を検出できる可能性の高さ |
設計改善と品質向上
FMEAは設計改善と品質向上に大きく貢献します。潜在的な故障モードを特定し、その原因と影響を分析することで、設計上の弱点や改善点を見つけ出すことができます。設計段階でこれらの問題に対処することで、製品の信頼性と耐久性を向上させることが可能です。また、製造プロセスにおける潜在的な問題点も明らかにし、品質管理の改善に役立てられます。
FMEAを通じて得られた知見は、設計変更やプロセス改善に直接反映されます。例えば、特定の部品の故障モードが頻繁に発生する場合、その部品の材質や設計を見直すことができます。また、製造プロセスにおける特定の工程が品質に悪影響を与えている場合、その工程の改善や自動化を検討できます。これらの改善活動を通じて、製品全体の品質向上を実現します。
改善の種類 | 具体的な対策 |
---|---|
設計変更 | 部品材質の変更や形状修正 |
工程改善 | 作業手順の見直しや自動化 |
品質管理 | 検査体制の強化や基準値設定 |
予防保全 | 定期的な点検や部品交換 |